14 IMPORTANT ENGINEERING PROPERTIES OF AGGREGATES USED IN CONCRETE
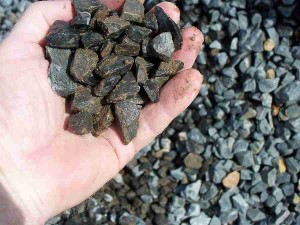
ENGINEERING PROPERTIES OF AGGREGATES
Aggregates are used in concrete to provide economy in the cost of concrete. Aggregates act as filler only. These do not react with cement and water.
But there are properties or characteristics of aggregate which influence the properties of resulting concrete mix. These are as follow.
- Composition
- Size & Shape
- Surface Texture
- Specific Gravity
- Bulk Density
- Voids
- Porosity & Absorption
- Bulking of Sand
- Fineness Modulus of Aggregate
- Surface Index of Aggregate
- Deleterious Material
- Crushing Value of Aggregate
- Impact Value of Aggregate
- Abrasion Value of Aggregate
1. COMPOSITION
Aggregates consisting of materials that can react with alkalies in cement and cause excessive expansion, cracking and deterioration of concrete mix should never be used. Therefore it is required to test aggregates to know whether there is presence of any such constituents in aggregate or not.
2. SIZE & SHAPE
The size and shape of the aggregate particles greatly influence the quantity of cement required in concrete mix and hence ultimately economy of concrete. For the preparation of economical concrete mix on should use largest coarse aggregates feasible for the structure. IS-456 suggests following recommendation to decide the maximum size of coarse aggregate to be used in P.C.C & R.C.C mix.
Maximum size of aggregate should be less than
- One-fourth of the minimum dimension of the concrete member.
- One-fifth of the minimum dimension of the reinforced concrete member.
- The minimum clear spacing between reinforced bars or 5 mm less than the minimum cover between the reinforced bars and form, whichever is smaller for heavily reinforced concrete members such as the ribs of the main bars.
Remember that the size & shape of aggregate particles influence the properties of freshly mixed concrete more as compared to those of hardened concrete.
3. SURFACE TEXTURE
The development of hard bond strength between aggregate particles and cement paste depends upon the surface texture, surface roughness and surface porosity of the aggregate particles.
If the surface is rough but porous, maximum bond strength develops. In porous surface aggregates, the bond strength increases due to setting of cement paste in the pores.
4. SPECIFIC GRAVITY
The ratio of weight of oven dried aggregates maintained for 24 hours at a temperature of 100 to 1100C, to the weight of equal volume of water displaced by saturated dry surface aggregate is known as specific gravity of aggregates.
Specific gravities are primarily of two types.
- Apparent specific gravity
- Bulk specific gravity
Specific gravity is a mean to decide the suitability of the aggregate. Low specific gravity generally indicates porous, weak and absorptive materials, whereas high specific gravity indicates materials of good quality. Specific gravity of major aggregates falls within the range of 2.6 to 2.9.
Specific gravity values are also used while designing concrete mix.
5. BULK DENSITY
It is defined as the weight of the aggregate required to fill a container of unit volume. It is generally expressed in kg/litre.
Bulk density of aggregates depends upon the following 3 factors.
- Degree of compaction
- Grading of aggregates
- Shape of aggregate particles
6. VOIDS
The empty spaces between the aggregate particles are known as voids. The volume of void equals the difference between the gross volume of the aggregate mass and the volume occupied by the particles alone.
7. POROSITY & ABSORPTION
The minute holes formed in rocks during solidification of the molten magma, due to air bubbles, are known as pores. Rocks containing pores are called porous rocks.
Water absorption may be defined as the difference between the weight of very dry aggregates and the weight of the saturated aggregates with surface dry conditions.
Depending upon the amount of moisture content in aggregates, it can exist in any of the 4 conditions.
- Very dry aggregate ( having no moisture)
- Dry aggregate (contain some moisture in its pores)
- Saturated surface dry aggregate (pores completely filled with moisture but no moisture on surface)
- Moist or wet aggregates (pores are filled with moisture and also having moisture on surface)
8. BULKING OF SAND
It can be defined as in increase in the bulk volume of the quantity of sand (i.e. fine aggregate) in a moist condition over the volume of the same quantity of dry or completely saturated sand. The ratio of the volume of moist sand due to the volume of sand when dry, is called bulking factor.
Fine sands bulk more than coarse sand
When water is added to dry and loose sand, a thin film of water is formed around the sand particles. Interlocking of air in between the sand particles and the film of water tends to push the particles apart due to surface tension and thus increase the volume. But in case of fully saturated sand the water films are broken and the volume becomes equal to that of dry sand.
9. FINENESS MODULUS
Fineness modulus is an empirical factor obtained by adding the cumulative percentages of aggregate retained on each of the standard sieves ranging from 80 mm to 150 micron and dividing this sum by 100.
Fineness modulus is generally used to get an idea of how coarse or fine the aggregate is. More fineness modulus value indicates that the aggregate is coarser and small value of fineness modulus indicates that the aggregate is finer.
10. SPECIFIC SURFACE OF AGGREGATE
The surface area per unit weight of the material is termed as specific surface. This is an indirect measure of the aggregate grading. Specific surface increases with the reduction in the size of aggregate particle. The specific surface area of the fine aggregate is very much more than that of coarse aggregate.
11. DELETERIOUS MATERIALS
Aggregates should not contain any harmful material in such a quantity so as to affect the strength and durability of the concrete. Such harmful materials are called deleterious materials. Deleterious materials may cause one of the following effects
- To interfere hydration of cement
- To prevent development of proper bond
- To reduce strength and durability
- To modify setting times
Deleterious materials generally found in aggregates, may be grouped as under
- Organic impurities
- Clay , silt & dust
- Salt contamination
12. CRUSHING VALUE
The aggregates crushing value gives a relative measure of resistance of an aggregate to crushing under gradually applied compressive load. The aggregate crushing strength value is a useful factor to know the behavior of aggregates when subjected to compressive loads.
13. IMPACT VALUE
The aggregate impact value gives a relative measure of the resistance of an aggregate to sudden shock or impact. The impact value of an aggregate is sometime used as an alternative to its crushing value.
14. ABRASION VALUE OF AGGREGATES
The abrasion value gives a relative measure of resistance of an aggregate to wear when it is rotated in a cylinder along with some abrasive charge.
No comments:
Post a Comment